Sửa chữa Biến tần Máy nén khí| Linh kiện Biến tần| Sửa và Cài đặt Biến tần sử dụng cho máy nén khí | Chuyên lập trinh biến tần điều khiển máy nén khí.
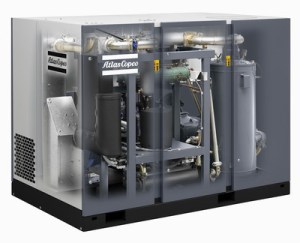
Sua bien tan may nen khi
Chuyên cung cấp dịch vụ bảo trì, sửa chữa Biến tần cho Máy nén khí. Vui lòng liên hệ Ban Quản trị để được tư vấn thêm.
Trong bài này, tôi xin phép được trình bày Nguyên lý của việc tiết kiệm điện năng trong các hệ thống Máy nén khí hiện nay.
I. Đặt Vấn Đề
Trong hệ thống đường ống cung cấp khí, đối tượng điều khiển cơ bản nhất là lưu lượng và áp suất khí. Nhiệm vụ cơ bản của hệ thống đường ống cung cấp khí nén là đáp ứng nhu cầu của người dùng về lưu lượng và áp suất. Nếu lưu lượng đủ nhưng áp không đủ–> Hiệu quả không cao. Nếu áp đủ, lưu lượng không đủ đáp ứng thì hệ thống vẫn chưa đạt tiêu chuẩn về khả năng khai thác thiết bị.

Sơ đồ nguyên lý máy nén khí trục vít
II. CHẾ ĐỒ ĐIỀU KHIỂN VÀ VẬN HÀNH
1. Chế độ Load/Unload:
Chế độ này cơ bản được hiểu như sau:
– Khi hệ thống sản xuất sd khí nén làm giảm áp trên đường ống, Động cơ đang hoạt động ở chế độ Không tải, tất cả van cửa vào ĐÓNG và khí không được nạp vào bình chứa.Sensor áp suất báo P < Pmin (đã cài đặt từ trước) là giới hạn áp suất nhỏ nhất cho phép, Bộ điều khiển xuất tín hiệu cho MỞ Van cửa vào và khí tiếp tục được nạp đến khi đủ áp suất giới hạn Pmax thì Đóng van cửa vào. Áp suất lúc này không tăng nữa. Động cơ vẫn chạy ở tốc độ định mức với f=50/60Hz.
Công suất động cơ trong các máy nén khí thường được chọn = Công suất sử dụng lớn nhất và thường là Dư tải. Các thiết bị sử dụng trong hệ thống thường là Contactor KĐ SAO-TAM GIÁC. Như vậy ta có thể ngầm hiểu là Nhà sản xuất không thể cho Động cơ dừng ở chế độ Unload vì thường là thời gian này tương đối nhỏ trong khi khoảng thời gian để động cơ khởi động xong lại lớn hơn. Thêm nữa nếu cứ cho Động cơ khởi động/dừng như vậy thì tuổi thọ Động cơ sẽ suy giảm đáng kể, Các thiết bị khởi động bị cháy hoặc hư tiếp điểm và gây ra hiện tượng sụt áp trên lưới.
Chế độ Load/Unload thường xuyên là nguyên nhân thay đổi áp suất trong toàn bộ đường ống, và áp suất làm việc không ổn định sẽ giảm tuổi thọ của máy nén khí. Mặc dù đã có một vài điều chỉnh cho máy nén khí (chẳng hạn như điều chỉnh van, điều chỉnh tải) ngay cả trong trường hợp lưu lượng ít, lượng điện tiêu thụ giảm xuống cũng không đáng kể do motor quay liên tục.
Đề xuất: Sử dụng thiết bị Điều khiển để cho tần số chạy Unload < tần số định mức ( VD: bằng 25Hz). Lý do :Công suất tiêu thụ của động cơ tỷ lệ bậc 3 với tốc độ quay P~n^3, khi tốc độ giảm 20%, công suất tiêu thụ chỉ còn khoảng 65-70% so với lúc đầy tải.
2. Chế độ điều khiển tốc độ quay motor
Điều chỉnh lưu lượng bằng cách thay đổi tốc độ quay của máy nén khí, trong khi vẫn giữ cho van mở không thay đổi (thường là duy trì mở tối đa). Khi tốc độ quay của máy nén khí thay đổi, các đặc tính khác cũng thay đổi cùng với hệ thống nén khí, trong khi lực cản đường ống không đổi.
Nguyên lý điều khiển tốc độ cơ bản nhất và phổ biến nhất hiện nay là V/f. Tốc độ động cơ được điều khiển thông qua bộ Biến tần: AC-DC-AC để đạt được tần số mong muốn. Khi đó áp suất khí cần tăng thêm trên đường ống sẽ phụ thuộc hoàn toàn vào tốc độ quay của động cơ và các Van cửa vào luôn ở trạng thái mở tối đa.
Ta có công thức như sau:
Q1 / Q2 = n1 / n2
H1 / H2 = (n1 / n2)2
P1 / P2 = (n1 / n2)^3
Ở đây:
Q: là lưu lượng khí cung cấp cho đường ống bởi máy nén khí.
H: là áp suất của hệ thống đường ống
P: công suất tiêu thụ của motor
n: tốc độ quay của máy nén khí
Vậy ở công thức số 3 (P~n^3): nếu ta giảm tốc độ quay của Động cơ đi 20% thì điện năng tiết kiệm có thể lên tới 40% ( đã trừ tổn hao).
Ở chế độ này, ta có hai PP để điều khiển, Chi tiết về Ưu/ Nhược điểm từng pp có thể coi ở bài viết trước của tôi tại ĐÂY
2.1 Phương pháp PID
Sử dụng Bộ điều khiển PID có tích hợp sẵn trong Biến tần và Tín hiệu phản hồi cho BĐK lấy từ Cảm biến Áp suất đưa trực tiếp về NGõ vào Analog của Biến tần (VD: Tín hiệu 0-10VDC)

Điều khiển PID sd Biến tần
Bộ điều khiển sé dựa vào áp suất thực tế từ cảm biến đưa về và so sánh với áp suất đặt để tăng/ giảm tốc độ động cơ.
2.2 Phương pháp đa cấp tốc độ, sd tín hiệu Load/Unload từ Solenoid.
Khi tín hiệu Load ON: Biến tần cho động cơ chạy ở tốc độ n1 = tốc độ định mức
Khi tín hiệu Unload ON: Biến tần cho động cơ chạy ở tốc độ n2 = tốc độ thấp hơn định mức khoảng 50%

Phương pháp chạy 2 cấp tốc độ
Ở cả hai phương pháp trên, phần trăm tiết kiệm điện năng phụ thuộc hoàn toàn vào thời gian và mức độ sử dụng tại nhà máy nhưng thông thường nằm trong khoảng 25-45%.
Hơn nữa Biến tần còn có một số chức năng bảo vệ, và giảm tối đa dòng KĐ so với Bộ KĐ Sao-Tam giác thông thường.
III. QUY TRÌNH THỰC HIỆN
1. Khảo sát hiện trạng và tư vấn tại nhà máy ( miễn phí )
2. Lên phương án, bản vẽ, thuyết minh kỹ thuật, chứng minh khả năng tiết kiệm ( miễn phí)
3. Báo chi phí và kế hoạch thực hiện ( miễn phí )
4. Ký hợp đồng cung cấp Dịch vụ
5. Triển khai dự án
6. Kiểm nghiệm thực tế tính khả thi ( miễn phí)
7. Nghiệm thu, bàn giao ( miễn phí)
8. Bảo trì, bảo dưỡng thường niên ( miễn phí trong 12 tháng)
Hãy liên hệ ngay với chúng tôi để nhận được những dịch vụ chu đáo nhất.